About
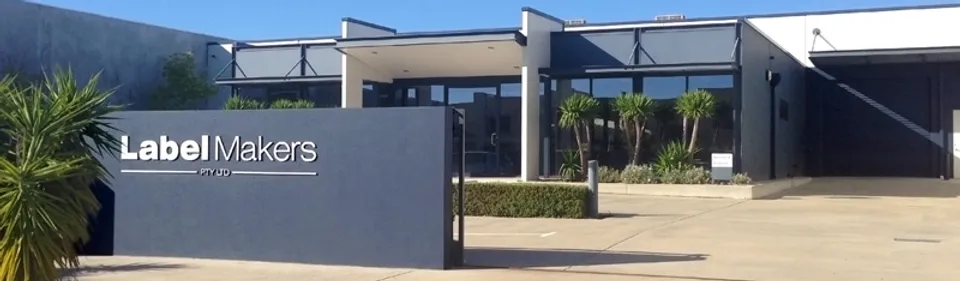
Formed in 1980 Label Makers Pty Ltd draws from over 40 years of self adhesive label and sticker printing industry experience to provide its clients with high quality cost effective label and sticker solutions – on time, and in full. Today we operate from a modern manufacturing facility in Perth, Western Australia, from which our first class label printing service is provided to clients – Australia wide. Most of our labels are made to order although we do hold some stock of common sizes, and dangerous goods labels on our shelfs. Every single label we supply is manufactured by us here in Australia!
Our team
Everything we do at Label Makers is underwritten by solid hands-on technical expertise covering all aspects of sticker printing, label manufacture and tag printing. Over the last 40 years we have grown to become one of the most respected and innovative label printing specialists in Australia and today we employ some of the best print professionals in the business.
Your team
At all stages our experienced staff manage your sticker printing projects and keep you posted with your jobs throughout the production process. Label Makers has developed the perfect team to produce your labels, to your standards, leaving you to concentrate on your core business. Our experts are on hand to help guide you through the process of selecting the most suitable solution for your needs. For more information about some of our processes please see our FAQs below.
To which states do Label Makers supply labels?
We supply labels to all states Australia wide. Our client base is wide and varied.
- Everyday we supply labels to customers in WA, SA, NSW, QLD, ACT, NT and Tasmania.
- Our sales team are often interstate visiting clients and offering support to our customer base. If you would like a visit contact us.
How does the order process work?
Your job will be processed in a manner along the lines of:
- Your needs – We discuss your needs with you, and you supply us with any artwork or data that’s relevant to the job.
- Pricing / delivery – Our sales team will produce a quotation for you and commit to a delivery time that is acceptable to you.
- Artwork approval – We will provide you with a proof of your print job for you to approve. This will only happen on first runs unless requested otherwise. Repeat orders are produced exactly as per the previous order.
- Manufacturing – Once approved we will order plates and dies if required, and manufacture your order to the highest achievable standards. Your job will be inspected and despatched as per your instructions. An invoice will be sent to you at the point of despatch.
What is four colour process (CMYK) printing?
Mixing all three theoretically results in black, but imperfect ink formulations do not give true black, which is why the additional K component is needed. We use this process for producing photographic type images with multiple colours and tones.
What is a spot colour?
What is a die cutter?
What kind of materials can you print on?
We can print on to virtually all commonly used substrates including but not limited to;
- Paper – General use, packaging and over-printable labels
- Polypropylene (PP) – Packaging and chemical labelling
- Polyesters (PET) – Speciality and security labels
- Polyethylene (PE) – Packaging labels
- Woven Fabrics – Textile labels
- Vinyl – Durable and outdoor labels
- Biaxially Orientated Polypropylene (BOPP) – Conformables and laminates
Our technically trained staff will be able to recommend the best substrates to you dependent on your requirements.
What is the delivery time for my labels?
What are roll directions and how do they affect me?
What finished format can you supply labels in?
We are able to supply labels in various formats including;
- On rolls using 1”, 1.5” and 3” cardboard cores. (We can even supply rolls core free if you wish)
- Sheets,
- Fan-folded collated packs
- Die cut singles.
- Stapled book form
- Shrink wrapped packs
- Rolls in dispenser cartons
Can I have a perforation between my labels?
Do you supply thermal printer labels?
We sure do. We supply a wide range of standard direct thermal and thermal transfer labels for all of the popular thermal printers, including;
- Zebra
- Sato
- Tec
- Datamax
- Intermec
Plus many more…. Just tell us your printer make and model and we’ll have all of the required information to hand.
What is the minimum order quantity?
Can we have our labels sequentially numbered?
in major volumes too. Typical numbering jobs can range from 5000 to 2 million labels at a time.
What format of bar code can I have?
We can supply a wide range of formats including but not limited to;
- Bar Code 2/5 interleaved: high density numeric, variable length, no checksum
- Bar Code 39: partial alpha-numeric, variable length, no checksum
- Bar Code 93: partial alpha-numeric, variable length, two checksums required
- Bar Code 128: alpha-numeric, plus numeric, variable length, checksum required
- Bookland: fixed length numeric, checksum required, encodes ISBN and price
- Codabar: numeric plus four alpha characters, variable length, no checksum
- EAN 8: 8 digit numeric, checksum required
- EAN 13: 13 digit numeric, checksum required, for retail products in Europe
- ISBN: fixed length numeric, checksum required, encodes ISBN and price
- ITF-14: fixed length numeric, checksum required, encodes GTIN
- SCC-14: Shipping Container Code, based on UPC
- SSCC-18: Serial Shipping Container Code, based on UPC and tracking number
- UPC-A: 12 digit numeric, checksum required, for retail products in North America
- UPC-E: 6 digit numeric, checksum required, for retail products in North America
- 2D Data Matrix and QR Codes – popular for retail promotional use and
- PDF 417 codes, low cost high capacity ID bar coding format.
We are able to integrate your own algorithm for check characters if you wish or we can use any of the standard routines too. We are able to advise you on the best format for your application if you are not sure.
What drives us
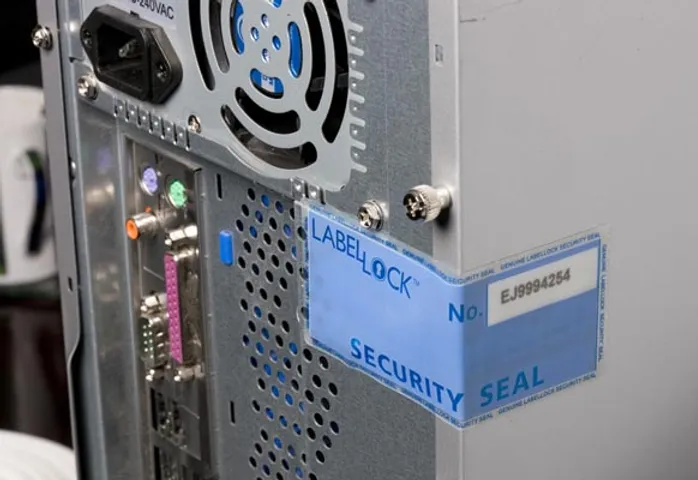
Track record
Our client list features many of Australia’s leading household names including retailers, manufacturers, meat industry organisations, growers, and service providers. We also service many public sector operations and professional bodies as well as nationwide government and educational organisations. We have been accredited with excellence awards from major corporate bodies, and preferred supplier status by some of Australia biggest retailers. We are HACCP certified, and Green Stamp accredited.

Technology
Label Makers are a technology driven company and this is reflected by the overall high levels of investment we have made in label printing plant and equipment, securing our position as market leaders and providing our client base with the best quality and most cost efficient solutions available. We operate fast, efficient and reliable equipment minimising down time, and ensuring you get the highest standards of quality.
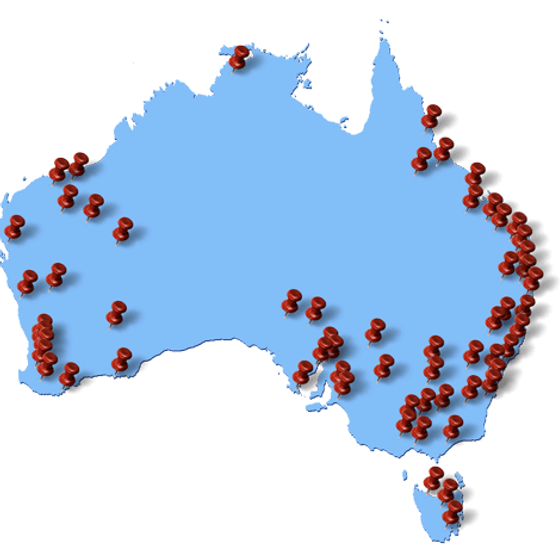
Nationwide suppliers
Label Makers are long established manufacturers and suppliers of self adhesive labels, stickers, tags and other printed packaging, supplying thousands of customers around Australia and New Zealand. Our client base stretches to all states of Australia, Tasmania, New Zealand, Malaysia and the Philippines.
Daily we supply self adhesive labels to a wide and varied australian customer base covering;
- Western Australia (WA)
- Victoria (VIC)
- New South Wales (NSW)
- Australian Capital Territory (ACT)
- Queensland (QLD)
- Northern Territory (NT)
- Tasmania (TAS)
- Adelaide (SA)
We serve remote locations and major cities all within our standard lead times. Our dedicated sales team regularly visit clients in all states to discuss large projects and supply solutions.